Toward a greener iron and steel industry
With the steel industry accounting for a significant portion of global CO2 emissions, calculating the technical and economic feasibility of future steel factories with reduced carbon emissions is vital in the transition toward a greener sector.
In recent years, the iron and steel industry has come under increasing pressure to address its carbon footprint. Accounting for 2.6 gigatons of global carbon dioxide emissions annually, steel production ranks as the largest industrial consumer of coal, surpassing emissions from all road freight combined. However, there are intrinsic limitations on decarbonizing this industry, leading to its classification as a hard-to-abate sector. To tackle this challenge, Prof. Valerie Eveloy, a professor of mechanical and nuclear engineering at Khalifa University, and her team are exploring low-carbon solutions for the iron and steel industry.
Hydrogen and renewables for the largest decarbonization potential
Among conventional steel-making processes, gas-based direct reduction of iron (DRI) combined with electric arc furnaces (EAFs) stands out as a relatively low carbon-intensive option. However, as of today, only 7% of global steel production uses these techniques.
In DRI, the reducing agent that strips away oxygen from iron or to leave behind metallic iron, has primarily been coal or natural gas so the DRI-EAF method has been predominantly deployed in regions with access to abundant and affordable natural gas. Prof. Eveloy and her team have modeled steel plants that use hydrogen as the reducing agent; a game-changing approach with immense potential for achieving net zero emissions, particularly when hydrogen is produced from water, generating oxygen and heat as byproducts.
“Energy-intensive industries, such as steel making, are in the midst of profound changes. Steel producers in the region are turning their attention to low-carbon hydrogen produced with minimal greenhouse gas emissions or carbon dioxide footprint, alongside efforts to improve energy and material efficiency.”
Prof. Valerie Eveloy
The researchers assessed the effectiveness and cost of hydrogen DRI-EAF in various locations where solar and/or wind energy could power hydrogen production and electrified processes. They found that, under favorable conditions, hydrogen DRI-EAF could compete economically with conventional processes and offer up to 90% reduction in CO2 emissions.1,2 With significant international attention, large-scale commercialization is expected to begin in the next decade.
“Energy-intensive industries, such as steel making, are in the midst of profound changes. Steel producers in the region are turning their attention to low-carbon hydrogen, alongside efforts to improve energy and material efficiency,” explains Eveloy.
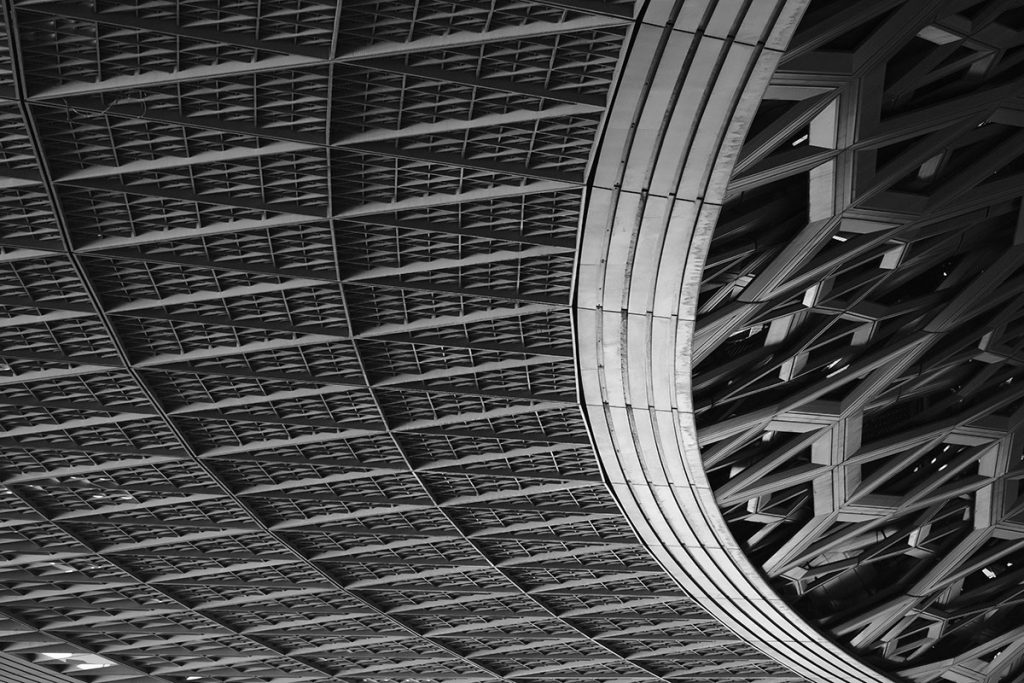
Addressing high emissions in traditional steel production
The most widely adopted process of steel production is the two-part process known as blast furnace-basic oxygen furnace (BF-BOF). It relies heavily on burning coke, derived from coal, to produce carbon monoxide, which reacts with iron ore and reduces it to molten iron and CO2. Oxygen is then blown into the molten iron at a high temperature and pressure to remove impurities and produce crude steel. This process emits significant amounts of carbon dioxide due to the large quantities of coke and energy used.
Eveloy’s team, alongside researchers from the University of Zaragoza in Spain, has looked at ways to overcome the high carbon emissions using power-to-gas technology, a way to produce a synthetic gaseous fuel (methane) using green hydrogen from water electrolysis and CO2 from steelmaking, using electric power. They analyzed how the integration of power-to-methane in the BF-BOF process could reduce its carbon footprint and how this would affect costs.
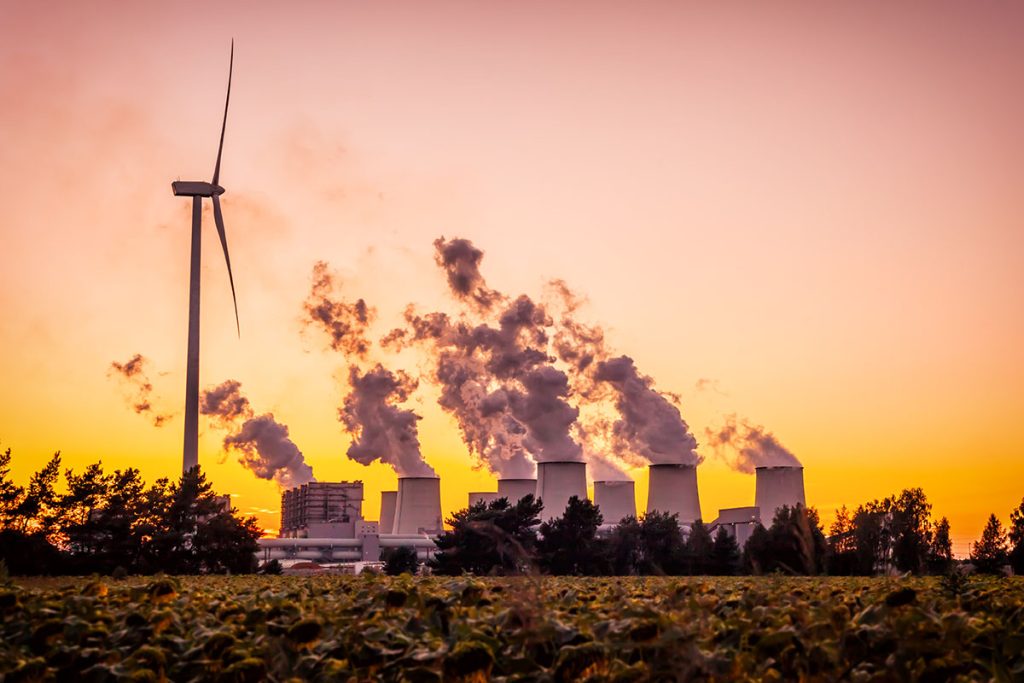
Injecting methane into the blast furnace as a fuel directly replaces some of the coke. Furthermore, as part of the power-to-gas process, CO2 emissions generated in the plant are captured for producing the methane, recycling in the same plant. The oxygen generated in the electrolysis of water in the power-to-gas process can meet the entire oxygen demand of a steel-making plant, eliminating the need for an energy-intensive air separation process to provide it.3
Integrating these technologies into traditional steel production could slash the carbon emissions of a steel plant by up to 34%. However, there is a trade-off: extra energy is required (around 17 megajoules per ton of hot metal) at extra cost (around USD378 per ton of carbon saved).4
Despite the high cost, the researchers remain optimistic about the economic feasibility of this concept. Fluctuating electricity prices and government subsidies aimed at combating climate change could significantly improve the viability of these technologies, especially as companies face the prospect of higher carbon taxes in the future.
References
1. Elsheikh H., Eveloy, V. Renewable Hydrogen based Direct Iron Ore Reduction and Steel Making with Grid Assistance. Energy Conversion and Management 297, 117544, 2023. | Article
2. Elsheikh H., Eveloy, V. Assessment of Variable Solar-and Grid Electricity-driven Power-to-hydrogen Integration with Direct Iron Ore Reduction for Low-carbon Steel Making. Fuel 324, 124758, 2022. | Article
3. Perpiñán, J., Bailera, M., Peña, B., Romeo, L.M., and Eveloy, V. Technical and economic assessment of iron and steelmaking decarbonization via power to gas and amine scrubbing. Energy 276, 127616, 2023. | Article
4. Perpiñán, J., Bailera, M., Peña, B., Romeo, L.M. and Eveloy, V. High oxygen and SNG injection in blast furnace ironmaking with Power to Gas integration and CO2 recycling. Journal of Cleaner Production 405, 137001, 2023. | Article